2025-05-28
Wire drawing molds are widely used in various industries
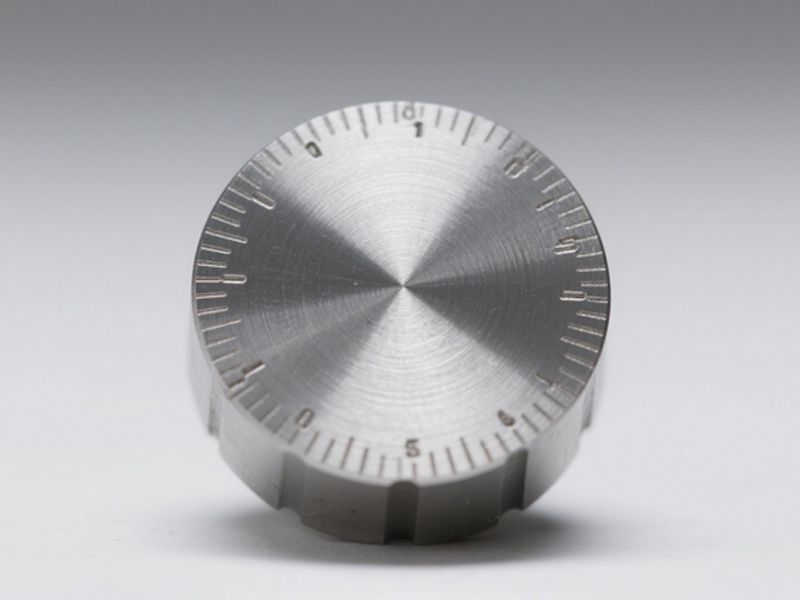
2025-05-28
Wire drawing molds achieve metal deformation through four working areas
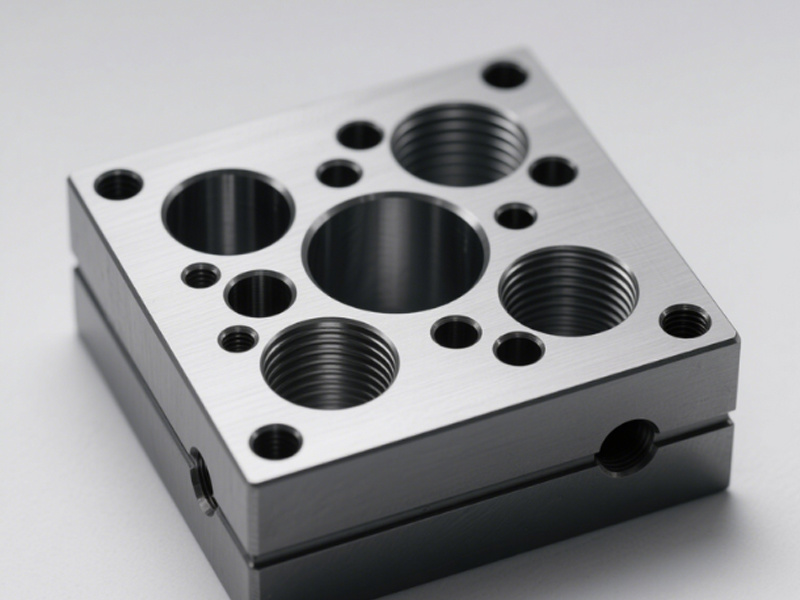
2025-05-28
Composition and structure of wire drawing molds
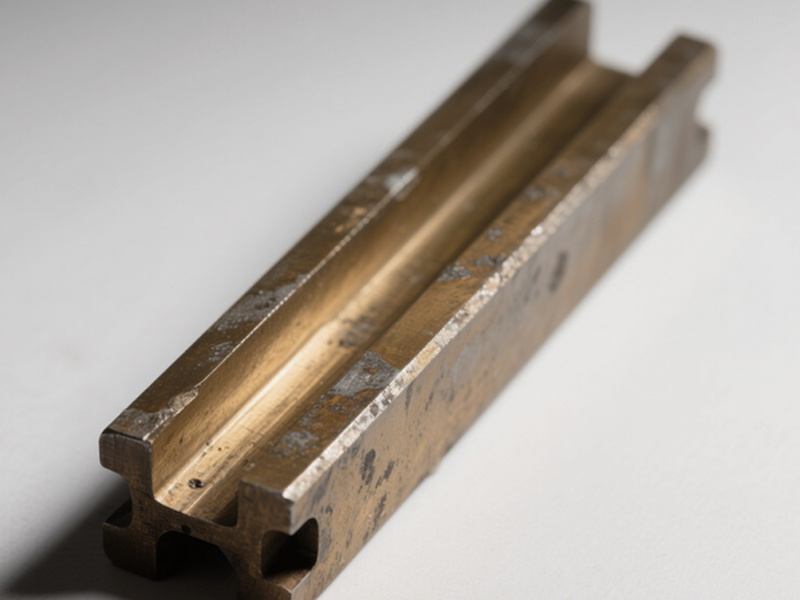
Application fields of nano diamond coated irregular molds
28
2025/05
Technical characteristics of nano diamond coated irregular molds
28
2025/05
Irregular conductor cable mold mold characteristics
12
2025/05
Preparation process of nano-diamond coated mold
12
2025/05
Technical characteristics of nano-diamond coated mold technology
12
2025/05
Key Application Areas of Special Shaped Wire Drawing Dies
12
2025/05
Core characteristics and classification of special-shaped wire drawing dies
12
2025/05